SIA Tech Brief: Applying Digital Twins to the Built Environment
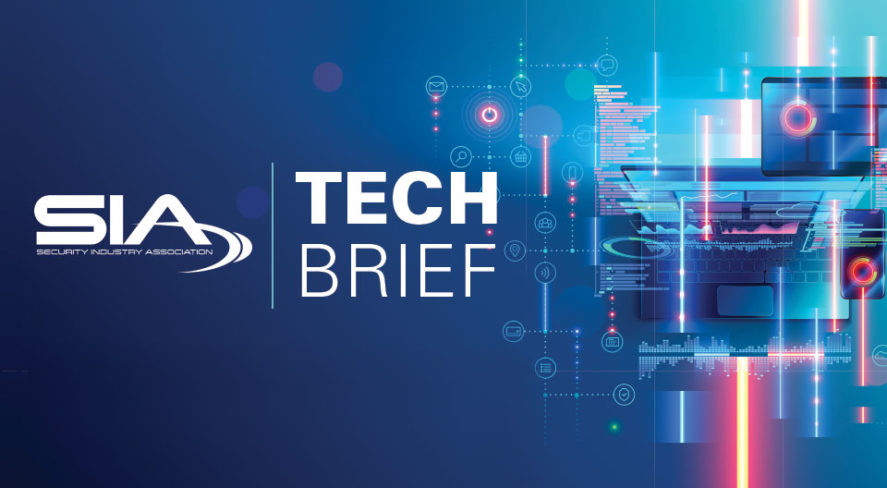
Introduction
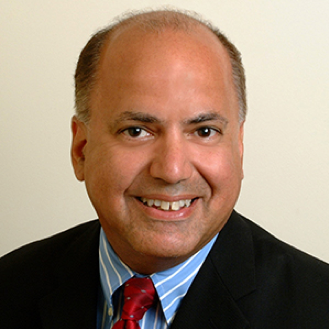
Digital twins turn the physical world into computable objects that track assets, people and processes. But what exactly is a digital twin? Defined by the Digital Twin Consortium, a digital twin is “a virtual representation of real-world entities and processes, synchronized at a specified frequency and fidelity.” Digital twins must have three characteristics:
- Why: Digital twin systems transform businesses by accelerating holistic understanding, optimal decision making and effective action.
- When: Digital twins use real-time and historical data to represent the past and present and simulate predicted futures.
- How: Digital twins are motivated by outcomes, tailored to use cases, powered by integration, built on data, guided by domain knowledge and implemented in IT/Internet of Things (IoT) systems.
Design and Construction Twins: Original Survey vs. Changes
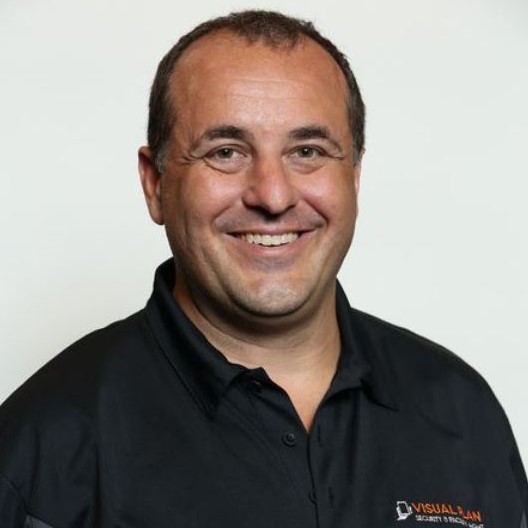
Preferably, the digital twin is created first, before or during construction and before its physical counterpart as a design twin. Long before construction begins, the architect creates the first version, and unlike legacy paper design drawings, the digital design can immediately become a simulated physical building. As the drawings and plans change, the digital twin design assets are updated to track construction progress, identify issues, log requests for information and incompatibilities and decide on rework or change orders if needed. Architectural and engineering firms such as AECOM heavily depend on virtual inspection to ensure code compliance during construction to minimize change orders and reduce the number site visits. The digital construction twin is also critical to commissioning, testing and completing punch lists.
The use of photogrammetry is frequently utilized from design through construction, replacing standard job site photography to better monitor change and catalog project stages. Comments and notes are tagged in the 360-degree imagery, providing a quick and effective capture method that requires very little training. A facility manager or design consultant can capture immersive imagery by using a 360-degree camera attached to a hard hat while touring the site. The design twin or construction twin may be associated with project management or scheduling tools, introducing various data points. The goal is to identify these project issues early, preventing costly mistakes and managing the differences between design and build.
For a security professional like Benjamin Butchko of Butchko ESI, digital twins play a role in effective risk assessment, communications with owners and critical thinking to enable effective security design prior to implementation of countermeasures such as surveillance, access control and other real-time sensor technologies. The value multiples when dealing with remote unmanned infrastructure like power substations, where Burns & McDonnell are leveraging digital twins to collaborate on security design projects at many sites over a longer period. The digital twin also has a large role to play in effective pre-incident planning and response and can be used forensically during reconstruction efforts.
The result is a more holistic understanding of how security impacts operations and the wider organization, as well as engagement of stakeholders in the planning, training and implementation processes.
“Today, the digital twin is no longer a concept, but a required deliverable for many end users. It is more interactive and reliable than previous 2D as-built drawings,” said Jon Polly, chief solutions officer for ProTecht Solutions Partners. “For many system integrators, it is a value-add to the customer and a necessary tool for proper support and maintenance. For the consultant, it is a valuable training tool when conducting employee training and awareness”.
Operational Twins: Interoperability With Operational Process
In post-commissioning, the digital twin grows increasingly more valuable. Operational processes like preventative maintenance can be efficiently and virtually planned to ensure remediation efforts are quickly and accurately addressed with a single site visit. Routine maintenance can be implemented consistently where connected IoT sensors, digital controls, SCADA data and/or connections to CMMS provide the operator critical information to troubleshoot, track and look up asset information that can be validated visually. The digital twin can assist in resolving false triggers and prevent unnecessary site visits. The “operational twin” enables subject matter experts, project managers, engineering and security consultants to remotely and virtually inspect, collaborate and provide critical feedback and oversight, creating financial and operating efficiencies.
Digital twins have significant value where the quick exchange of information is critical to accurate decision making and downtime is very costly to operations. In a case study with major oil and gas non-destructive testing (NDT) company Qi2 Elements, a 90-minute visual capture session performed pre- and post-inspection, saved nearly $500,000 per tank integrity inspection by reducing downtime. Precise decisions and planning are essential on these projects. 3D LiDAR is typically used prefabrication and to simulate execution of complex processes. 360-degree imagery is used for communicating changing environments and operational tasks.
Fault detection and diagnostics has been increasingly applied to the process of identifying, isolating and diagnosing building performance issues. Digital twins can include modeling airflow or energy usage through sensors and control points in the building automation system, assessing performance of HVAC systems before a fault occurs. In NDT, such as condition assessments, the digital twin is helpful in deciding a workflow path so that nothing is overlooked, and results can be geospatially located to communicate the findings. This visualization becomes critical to remediation by identifying, locating and viewing the issue area while also understanding its surrounding environment.
At the smart cities level, the impact of digital twins can be enormous, managing effective water flow, power grid supply and demand, communication or transportation network flow control and simulations. But the interoperability and centralization of data is critical. “Simply put, if the data doesn’t get to its recipient, is late, interferes with other sensor data transmission or does not allow the user to scale and meet demands, the city’s IoT tech is less useful, less sensible,” one of this paper’s authors previously wrote. “A safe and smart city’s digital twin will not only allow the city to predict slow-moving threats but determine readiness reaction in real time to catastrophic weather events, earthquakes, and, of course, cyber-readiness. Scenarios are built using output from AI processes and training data from other successful digital twin models.”
Summary of Benefits Through Digital Twins: Design/Build
- Compliance inspections
- Repeatable O&M and PM schedules
- Asset visualization & categorization
- Remotely work with service provider
- Monitoring operational change
- Locating issue areas from NDT reports
- Virtual preplanning remediation
- Reduced onboarding/training time
- Safety oversight and early detection
- A system of archive and record
- Project management and oversight
- Early issue detection and reporting
- Accurate and frequent updates of BIM and As-Builts
Summary of Benefits Through Digital Twins:
- Generative design simulation
- Validate and report inspection findings
- Virtual RFP process
- Remote SME collaboration
- Reduced site visits and associated risks
- Identify security & safety issues
- Complete system of archive and record
- Identify process/system inefficiencies
- Project management and oversight
- Early issue detection and reporting
- AI project monitoring
- LiDAR to BIM deviation analysis
- Change order and approvals
- Assist with punch lists